In the ever-evolving landscape of technology, the concept of "desifake" has emerged as a transformative force reshaping modern industries. Desifake refers to the integration of digital fabrication techniques, which are revolutionizing how products are imagined, designed, and manufactured. This phenomenon is not only redefining traditional manufacturing processes but also unlocking new possibilities for innovation and efficiency.
From additive manufacturing to advanced software-driven tools, digital fabrication is reshaping industries across the board. The adoption of these cutting-edge technologies is not only boosting productivity but also enabling businesses to create intricate designs that were previously unimaginable. By blending precision with creativity, digital fabrication is setting new standards for manufacturing excellence.
As we explore this topic further, you will uncover the significance of understanding desifake, its practical applications, and its profound impact on modern industries. By the end of this article, you will have a comprehensive understanding of how digital fabrication is steering the future of manufacturing and influencing global markets.
Read also:Marcus Rosner A Closer Look At His Life Career And Relationship With His Wife
Before we delve deeper, here's a quick preview of the topics we will cover:
Table of Contents
- What is Desifake?
- History of Digital Fabrication
- Key Technologies in Digital Fabrication
- Applications in Modern Industries
- Advantages of Desifake
- Challenges and Limitations
- Future Trends in Digital Fabrication
- Case Studies: Success Stories in Desifake
- Ethical Considerations in Digital Fabrication
- Conclusion and Call to Action
Exploring the Concept of Desifake
Desifake embodies the fusion of design and fabrication in the digital era, enabling the creation of highly complex products through advanced technologies. This innovative approach encompasses a wide range of techniques, including 3D printing, CNC machining, laser cutting, and more. These methods collectively empower manufacturers to produce goods with unmatched precision and efficiency.
The emergence of desifake has been driven by significant advancements in both software and hardware, allowing for the production of high-quality goods with minimal waste. Industries such as aerospace, automotive, and healthcare have particularly benefited from this approach, as it facilitates precision manufacturing and customization tailored to specific needs.
At its core, desifake signifies a paradigm shift in manufacturing, moving away from conventional methods and embracing digital solutions that enhance productivity and innovation. This evolution is redefining the way products are conceptualized and brought to life.
The Evolution of Digital Fabrication
Origins of Digital Fabrication
The roots of digital fabrication can be traced back to the mid-20th century when early computer-aided design (CAD) systems were first introduced. These pioneering systems laid the groundwork for integrating technology into manufacturing processes, setting the stage for future advancements.
Over the decades, the exponential growth in computing power and software capabilities has propelled digital fabrication to unprecedented heights. The advent of 3D printing in the 1980s marked a significant milestone, enabling rapid prototyping and production. This breakthrough opened doors to possibilities that were once considered unattainable.
Read also:Penn Badgley The Actor Behind The Enigmatic Joe Goldberg
Modern Developments and Global Trends
Today, digital fabrication technologies are more accessible than ever, with affordable desktop 3D printers and intuitive software available to professionals and hobbyists alike. This democratization of technology has sparked innovation across numerous sectors, empowering individuals and businesses to explore new frontiers.
According to a report by Grand View Research, the global digital fabrication market is projected to grow at a compound annual growth rate (CAGR) of 14.3% from 2022 to 2030. This growth is fueled by the rising demand for customized products and sustainable manufacturing practices, underscoring the transformative potential of this field.
Pillars of Digital Fabrication: Key Technologies
3D Printing: Revolutionizing Additive Manufacturing
3D printing, also known as additive manufacturing, stands as one of the most influential technologies in the realm of digital fabrication. This technique involves creating three-dimensional objects by layering materials based on digital models, offering unparalleled flexibility and precision.
- Supports a diverse range of materials, including plastics, metals, and ceramics, catering to various industry needs.
- Capable of producing intricate geometries with exceptional accuracy, making it ideal for complex designs.
- Cost-effective for small-scale production and prototyping, providing businesses with a competitive edge.
CNC Machining: Precision at Its Best
Computer Numerical Control (CNC) machining plays a crucial role in digital fabrication. This technology utilizes pre-programmed software to control machine tools, ensuring precise cutting and shaping of materials with remarkable consistency.
- Delivers high accuracy and repeatability, ensuring consistent quality in production.
- Compatible with a wide array of materials, including metals and composites, expanding its application scope.
- Capable of producing large-scale components, meeting the demands of various industries.
Applications of Desifake Across Modern Industries
Aerospace Industry: Lightweight Innovation
The aerospace sector has fully embraced digital fabrication to produce lightweight and durable components. Companies like Boeing and Airbus leverage 3D printing to manufacture aircraft parts, significantly reducing weight and enhancing fuel efficiency. This approach not only optimizes performance but also lowers operational costs.
Healthcare Sector: Customized Solutions for Better Outcomes
In the healthcare industry, digital fabrication is transforming the production of medical devices and prosthetics. Through 3D printing, customized implants and prosthetic limbs can now be crafted with precision, offering improved fit and functionality for patients. This innovation is revolutionizing patient care and enhancing quality of life.
Automotive Manufacturing: Accelerating Innovation
The automotive industry harnesses digital fabrication for rapid prototyping and the production of intricate components. This technology enables manufacturers to test and refine designs more efficiently, expediting the development process and reducing time-to-market for new vehicles. The result is faster innovation and enhanced competitiveness.
The Benefits of Embracing Desifake
Increased Efficiency: Streamlining Manufacturing Processes
One of the standout advantages of desifake is the substantial improvement in manufacturing efficiency. By automating processes and minimizing waste, businesses can achieve higher productivity while reducing costs. This efficiency boost is a game-changer for industries striving to remain competitive in a fast-paced global market.
Enhanced Customization: Meeting Unique Customer Needs
Desifake empowers manufacturers to offer greater customization, enabling the production of unique products tailored to individual preferences. This capability is particularly valuable in industries such as fashion and healthcare, where personalized solutions are in high demand. By catering to specific customer needs, businesses can differentiate themselves and build stronger relationships with their clients.
Sustainability: A Path Toward Environmental Responsibility
Digital fabrication promotes sustainable manufacturing practices by minimizing material waste and reducing energy consumption. This commitment to sustainability aligns with global efforts to combat climate change and foster environmental responsibility. By adopting eco-friendly practices, industries can contribute to a more sustainable future while meeting regulatory requirements.
Navigating the Challenges of Desifake
High Initial Costs: A Barrier to Entry
While the long-term benefits of desifake are undeniable, the initial investment required to implement digital fabrication technologies can be substantial. This financial hurdle may pose challenges for small and medium-sized enterprises (SMEs), limiting their ability to adopt these transformative solutions. Overcoming this barrier requires strategic planning and access to affordable financing options.
Material Limitations: Expanding Possibilities
Although the range of materials compatible with digital fabrication continues to expand, certain materials remain difficult to work with using current technologies. This limitation can restrict the scope of applications in some industries, necessitating ongoing research and development to address these challenges. Innovations in material science will be key to unlocking the full potential of digital fabrication.
Skill Gap: Building a Skilled Workforce
The adoption of digital fabrication demands specialized skills and expertise, which may not be readily available in the workforce. Bridging this skill gap through comprehensive training programs and educational initiatives is essential for the widespread adoption of these technologies. By investing in workforce development, industries can ensure they have the talent needed to thrive in the digital age.
Emerging Trends in Digital Fabrication
AI Integration: Enhancing Automation and Decision-Making
The integration of artificial intelligence (AI) in digital fabrication is poised to revolutionize automation and decision-making processes. AI-driven systems can optimize production workflows, predict maintenance needs, and improve overall efficiency. This synergy between AI and digital fabrication will unlock new levels of productivity and innovation.
4D Printing: Beyond the Third Dimension
4D printing, an emerging technology that builds on 3D printing principles, involves creating objects capable of changing shape or function over time. This innovation holds immense promise for applications in smart materials and adaptive structures, opening doors to possibilities that were once the stuff of science fiction. As research progresses, 4D printing could become a cornerstone of future manufacturing.
Sustainable Materials: Paving the Way for Eco-Friendly Solutions
As environmental concerns continue to grow, the development of sustainable materials for digital fabrication is becoming a top priority. Researchers are actively exploring biodegradable and recyclable options to reduce the ecological footprint of manufacturing processes. By prioritizing sustainability, industries can contribute to a healthier planet while meeting consumer demand for eco-friendly products.
Real-World Success Stories in Desifake
Case Study 1: GE Additive – Transforming Aviation
General Electric (GE) has successfully integrated additive manufacturing into its aviation division, producing fuel nozzles for jet engines. This initiative has resulted in a 25% reduction in weight and a 50% decrease in the number of components, significantly improving fuel efficiency and overall performance. GE's success highlights the transformative potential of digital fabrication in the aerospace industry.
Case Study 2: Local Motors – Redefining Automotive Manufacturing
Local Motors, a pioneering U.S.-based automotive company, has revolutionized car manufacturing through the use of 3D printing. Their flagship vehicle, the Strati, was produced using a large-scale 3D printer, demonstrating the feasibility of digital fabrication in automotive production. This groundbreaking achievement showcases the potential of these technologies to reshape the industry.
Ethical Implications of Digital Fabrication
Intellectual Property: Protecting Original Creations
The rise of digital fabrication raises important questions about intellectual property rights. As 3D printing and other technologies make it easier to replicate designs, safeguarding original creations becomes increasingly challenging. Striking a balance between innovation and protection is critical to fostering a fair and competitive marketplace.
Workforce Displacement: Addressing the Human Factor
The automation enabled by digital fabrication may lead to job displacement in certain sectors, prompting concerns about the future of work. It is imperative for businesses and governments to address this issue through retraining programs and policy interventions. By equipping workers with the skills needed for the digital age, industries can mitigate the adverse effects of automation.
Environmental Impact: Balancing Innovation with Responsibility
While digital fabrication promotes sustainability, the production of certain materials and the energy consumption of some technologies can have negative environmental effects. Achieving a balance between innovation and environmental responsibility is a key challenge for the industry. By prioritizing eco-friendly practices, businesses can contribute to a more sustainable future.
Conclusion: Embracing the Future of Manufacturing
Understanding desifake and the rise of digital fabrication in modern industries is essential for businesses aiming to stay ahead in a rapidly changing world. This transformative technology offers numerous advantages, including enhanced efficiency, customization, and sustainability, while also presenting challenges that require thoughtful solutions.
We encourage you to explore further resources on digital fabrication and consider how these technologies can be applied in your industry. Share your thoughts and experiences in the comments below, and don't hesitate to explore other articles on our website for deeper insights into cutting-edge technologies shaping the future of manufacturing.
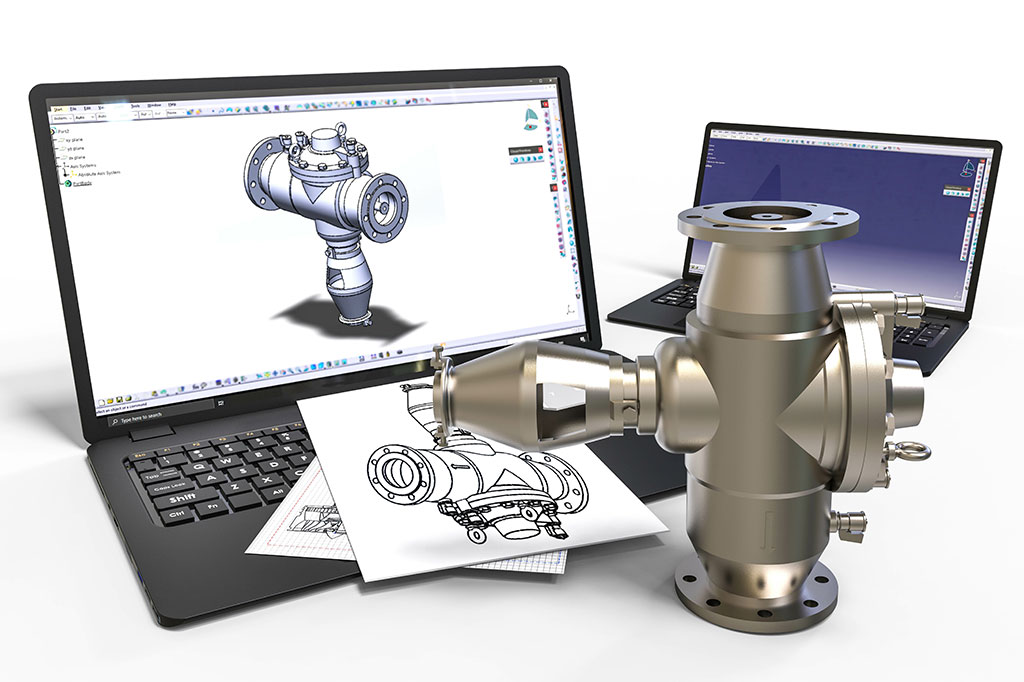
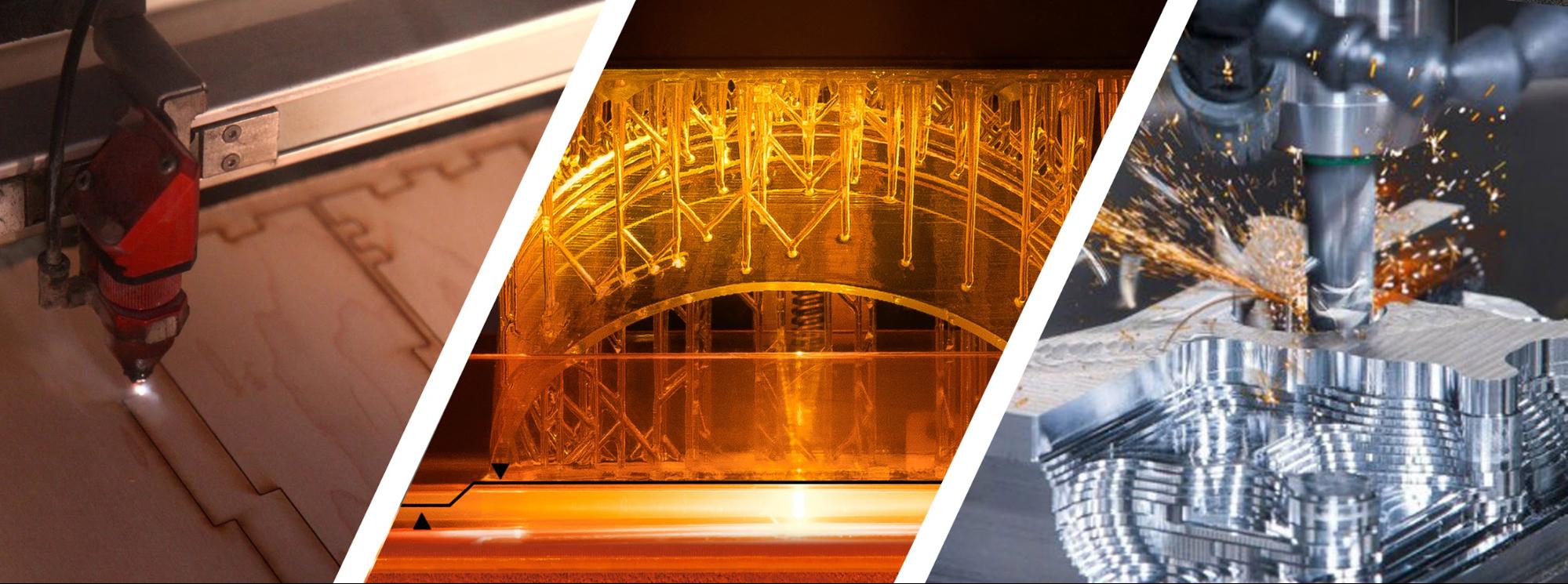
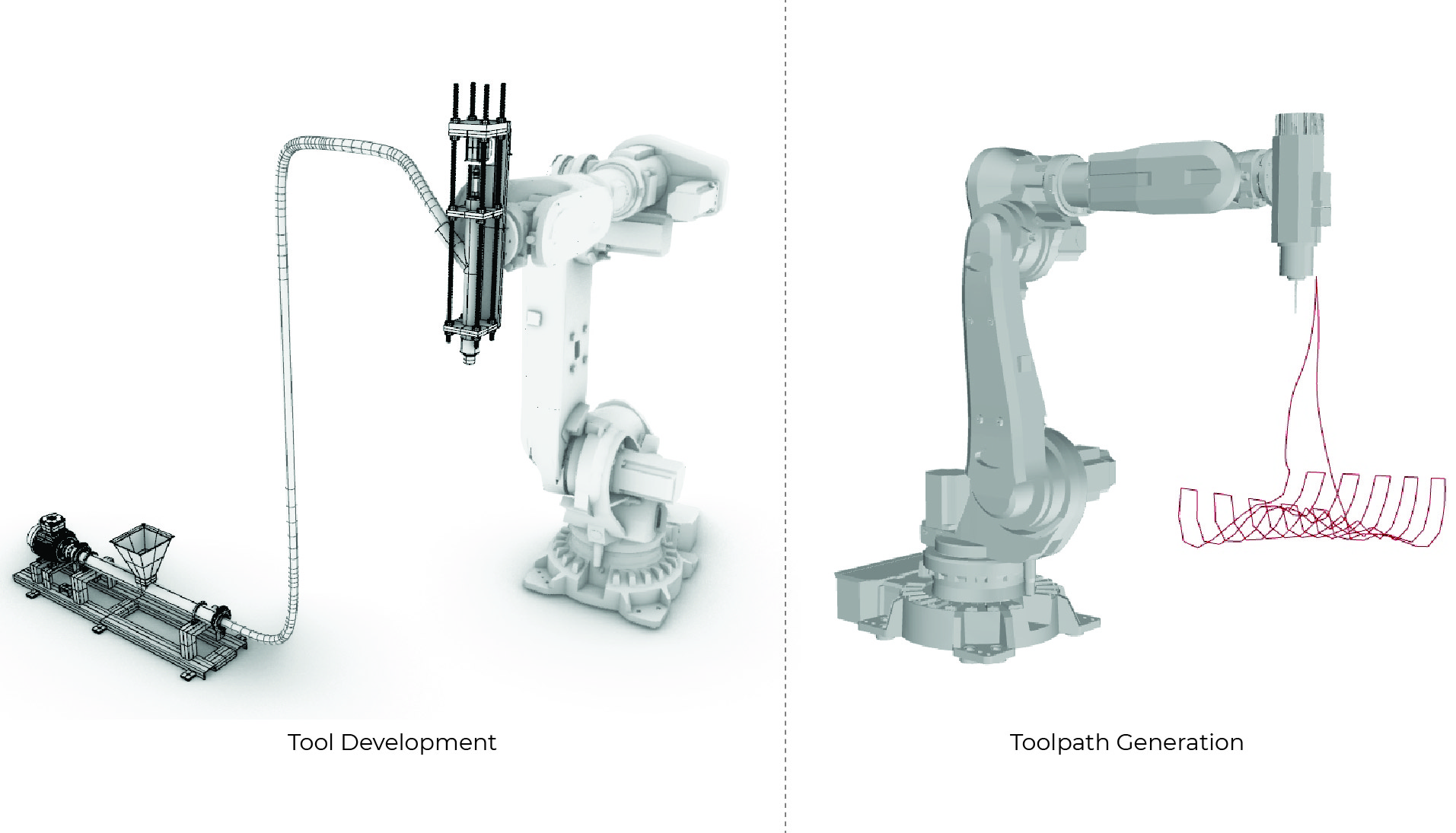